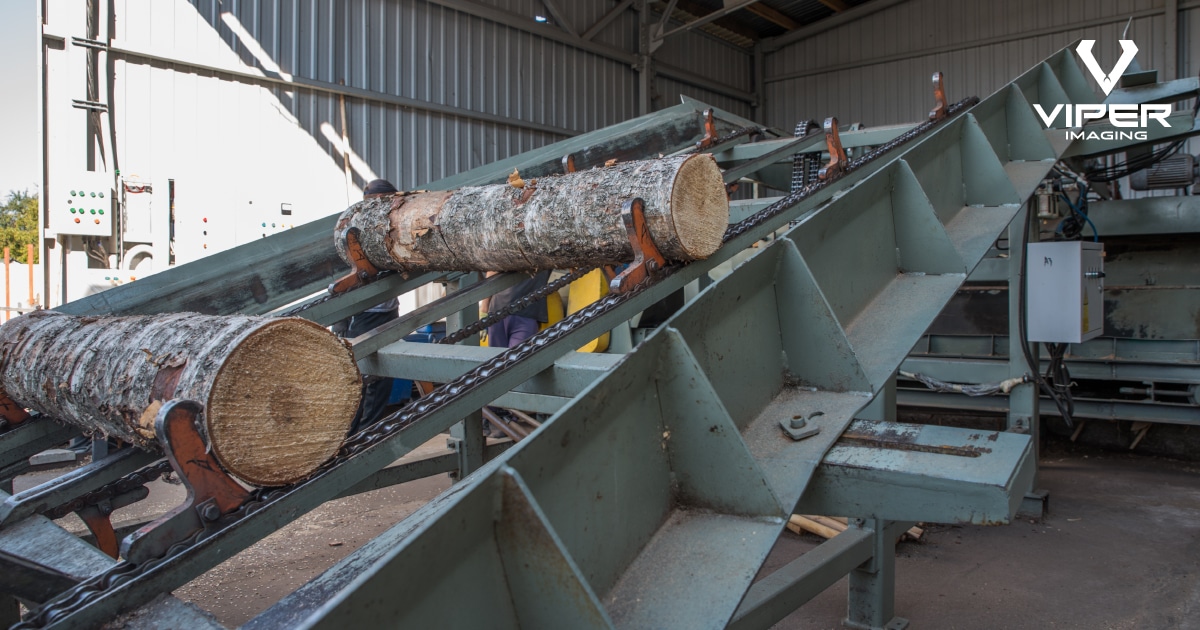
The lumber and wood processing industry is especially vulnerable to the catastrophic damage of fires and various fire hazards. Flammable materials, high temperatures, friction, and sparks create ideal conditions for fires to start and spread.
Most lumber mills, sawmills, and wood products manufacturers already have a range of fire systems in place. While these systems are necessary for safety and compliance, they are inherently reactive solutions that trigger only when a fire has started.
To reduce risk, lumber and wood processing facilities must proactively approach fire detection and prevention.
To learn more about how your facility can benefit from Continuous Thermal Monitoring solutions, download our latest white paper: Mitigating The Risk of Fires – Why Lumber and Wood Processing Facilities Need Continuous Thermal Monitoring.
How Fire Hazards Start in Lumber & Wood Processing Facilities
In a recent report, the National Fire Protection Association (NFPA) recorded more than 36,000 fires at industrial or manufacturing facilities, which caused more than $1.5 billion in direct property damage.
Fires are most likely to occur in areas difficult for maintenance personnel to access, inspect, and keep clear of debris. In wood processing facilities, fires commonly ignite in planer rooms, cutting areas, bulk storage facilities, and other areas where heavy equipment operates at high temperatures.
Fires can also occur outside of regular working hours long after the equipment has been shut down and workers have left the site. High equipment temperatures can linger next to flammable materials, leading to fire risks that can cause serious damage before emergency services arrive.
Combustible Dust Accumulation
Sawdust is a type of combustible dust that is highly flammable and can be explosive if suspended in the air. A dust cloud can form from sawdust, posing significant fire risks due to its potential for ignition. A report from British Columbia attributed sawdust as the first material to ignite in more than half of all sawmill fires. More than three-quarters of those fires were ignited by sparks or friction heat.
Continuous Thermal Monitoring solutions identify localized heating in dust-prone areas such as dust collection systems, ventilation ducts, and other processing equipment to allow operators to intervene before ignition occurs.
Spontaneous Combustion and Dust Explosion
Wood chips, sawdust, and other materials are often stored in large piles, bins, or silos before being used. These piles or layers act as insulators, trapping heat caused by oxidation and friction until it builds up and reaches the material’s self-ignition point. If this heat buildup is not detected and managed, it can lead to a dust explosion.
Continuous Thermal Monitoring solutions can detect heat variations that could indicate a thermal event. The detection capability is even better when combined with other sensors, such as embedded thermocouples or temperature probes.
Overheating Equipment & Sparks
Lumber and wood processing facilities operate heavy equipment such as saws, conveyors, sanders, planers, and dryers that can heat up and remain at high temperatures long after workers leave. Airborne particles from sawdust can contribute to fire risks when equipment overheats.
When examining the cause of fires, the NFPA report found that mechanical failure and equipment malfunction were among the leading factors. Thermal cameras detect unusual temperature spikes, often preceding equipment failure or sparks.
Electrical Fires
While steps have been taken in recent years to upgrade electrical equipment and wiring, electrical fires are still one of the leading causes of fires in industrial manufacturing facilities.
Aging and poorly maintained wiring, overloaded circuits, faulty connections, and other potential fire hazards can all lead to arching or sparks that ignite combustible materials. Continuous Thermal Monitoring can identify abnormal heat patterns in electrical distribution systems, connection points, and power transfer equipment before ignition occurs.
Hot Work Operations
Hot work operations include welding, cutting, grinding, and other tasks that produce heat, flames, or sparks. Thermal monitoring can be used before and after hot work operations to detect any residual heat and identify areas at risk of ignition. Proper handling of hot work operations is essential to prevent fires.
Mitigating the Risk of Fire
The lumber and wood processing sector is particularly vulnerable to fire. Flammable materials, fine wood dust, wood chips, and other byproducts of the manufacturing process mean that even small fires can quickly grow into an out-of-control blaze that damages equipment and threatens workers’ safety.
Continuous Thermal Monitoring solutions from Viper Imaging take a proactive approach by automatically detecting hazardous conditions before ignition. This allows facilities to take immediate action to prevent fires from starting. Regular fire drills should also be conducted as part of a comprehensive fire prevention strategy to ensure employees are familiar with emergency protocols and evacuation routes.
By leveraging advanced thermal cameras, lumber and wood processing companies can reduce downtime, enhance worker safety, and mitigate the risk of fires at their facilities. To see how you can deploy Continuous Thermal Monitoring solutions in your facility, download the white paper: