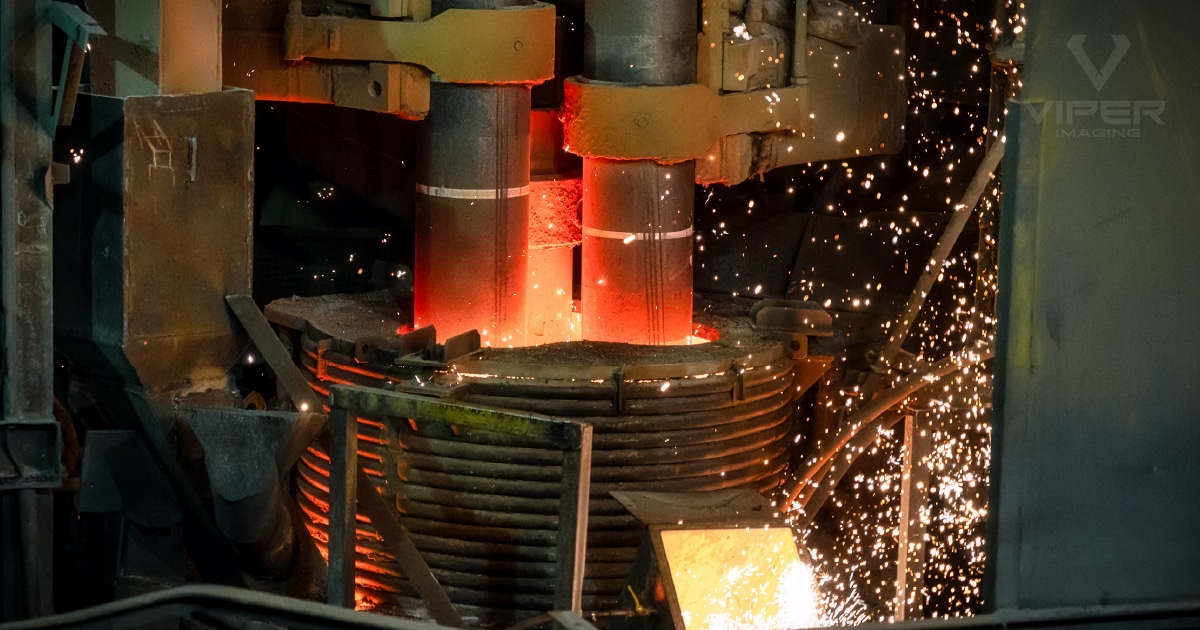
The steel industry has always embraced innovation. However, many critical processes still rely on physical inspections and scheduled maintenance strategies, which increase the likelihood of catastrophic equipment failure.
The steel industry has always embraced innovation. However, many critical processes still rely on physical inspections and scheduled maintenance strategies, which increase the likelihood of catastrophic equipment failure.
Ladle monitoring and Electric Arc Furnace (EAF) monitoring applications, for example, require highly skilled technicians to access the site, assess wear, and evaluate the condition of equipment.
Instead, steel manufacturers need a new solution that allows Operators to see real-time thermal and visual data from a safe, centralized location. Continuous Thermal Monitoring solutions leverage advanced thermal and visual cameras to provide steel plants with 24/7 coverage of ladles, electric arc furnaces, and other critical equipment. Prioritizing key equipment for thermal monitoring is essential to maximize reliability and safety in steel plant operations.
With greater visibility into the actual condition of assets, steel plants can reduce the risk of breakouts, optimize maintenance schedules, and improve workplace safety. Integrating thermal imaging with other maintenance technologies, such as vibration analysis or ultrasound, provides a more comprehensive view of asset health. Bringing all maintenance data into the same computer system enables unified reporting and improved decision-making for asset management.
To learn more about the benefits of Continuous Thermal Monitoring solutions, download our recent white paper: Mitigating Risk in the Steel Industry – The Benefits of Continuous Thermal Monitoring.
Thermal imaging as part of a predictive maintenance strategy can deliver significant cost savings by reducing unplanned downtime and minimizing operational expenses.
1. Mitigating the Risk of Ladle Breakouts
Ladles are critical for transporting and refining molten steel. However, they also present several maintenance challenges that must be addressed to ensure their safe and reliable operation. Breakouts are among the most dangerous and costly failures that can occur in steel manufacturing, and they can lead to injury or death if workers are exposed to molten materials.
Continuous Thermal Monitoring solutions reduce the risk of breakouts by providing real-time thermal data to operations and maintenance teams. Mounted thermal cameras measure external ladle temperature profiles to detect uneven heating or hotspots that may indicate refractory degradation. Maintenance technicians analyze thermal images from these cameras to identify potential issues before they escalate. Instead of waiting for an inspection, Operators can immediately stop production and initiate a repair.
Early detection through thermal monitoring helps avoid costly emergency repairs.
2. Optimizing Relining Intervals
Determining the optimal relining frequency is a complex and imprecise science that varies based on several factors. Relining too often increases costs and leads to unnecessary downtime, while delays can lead to degradation of the refractory lining and breakouts.
Continuous Thermal Monitoring provides real-time data on refractory wear, hot spots, and operational efficiency. Instead of relying on rough estimates, steel plants can optimize relining schedules based on the actual condition of the refractory lining. Scheduling maintenance based on real-time data is a key part of an effective maintenance program, enabling proactive and preventive strategies that minimize unplanned outages. This allows for partial repairs to localized, high-wear areas, rather than unnecessary full relines. Not only does this extend the life of the ladle, but it also enables steel plants to schedule relining during convenient windows, thereby reducing downtime.
Optimizing relining intervals as part of a structured maintenance program helps reduce equipment repair costs by preventing severe damage and avoiding costly emergency repairs.
3. Preventing EAF Steam Explosions
EAFs have revolutionized the steel production process, offering greater flexibility, energy efficiency, and sustainability compared to traditional blast furnaces. However, they also create unique risks and operational challenges that require specialized expertise. EAFs are part of the plant’s critical infrastructure and require advanced monitoring to ensure safe and reliable operation.
Water-cooled panels prevent the furnace shell and roof from overheating, while other cooling systems protect critical components such as the transformer, hydraulic actuators, and electrodes. Even small leaks can trigger a steam explosion, resulting in injuries, production shutdowns, and costly repairs.
Thermal sensors monitor the EAF shell, roof, panel, and electrode temperatures to provide early warning of water leaks from the cooling system. These condition monitoring sensors provide valuable data on equipment health by continuously assessing temperature changes and correlating measurements to identify potential issues. The sensors automatically detect a sudden or localized temperature drop that could indicate a leak, initiating an emergency shutdown to prevent water from reaching the molten steel. Early detection of leaks helps avert safety hazards for workers.
4. Detecting Furnace Wall Failure
The refractory lining of the EAF wall is repeatedly exposed to extreme temperatures. Each heat cycle expands and contracts the lining, weakening its structure and leading to localized failures. Thermal anomalies detected by sensors can indicate early signs of wear, allowing for timely intervention. Similarly, molten slag can react with the lining and break down protective materials.
Thermal sensors continuously track furnace wall temperatures to detect hot spots and signs of localized wear. Operators can use this data to identify thin refractory zones before they lead to collapse, shut down the EAF, and conduct partial repairs to the affected panels. By comparing heat signatures over time, operators can identify abnormal patterns that may signal the development of issues. As heat-producing friction develops in worn areas, temperature increases can be detected early with thermal monitoring.
The Benefits of Continuous Thermal Monitoring
Continuous Thermal Monitoring solutions equip Operators with real-time temperature data, enabling them to proactively identify faults and take corrective action before catastrophic failure occurs. Predictive maintenance and preventive maintenance are key components of modern maintenance programs that utilize thermal monitoring sensors to monitor equipment performance, minimize unplanned downtime, and enhance overall asset reliability.
Many steel manufacturers start by deploying cameras to monitor a specific asset or production process. This pilot project helps their personnel become familiar with the solution’s features and capabilities before expanding into additional facilities or applications.
A strong maintenance investment strategy includes tracking total maintenance costs and maintenance dollars to assess the return on investment of predictive and preventive maintenance programs. According to the federal energy management program, organizations that monitor and analyze these costs can achieve significant cost savings and improved return on investment (ROI) by implementing advanced maintenance technologies.
Predictive maintenance programs and preventive maintenance programs help save money by reducing maintenance fees, unplanned downtime, and unplanned equipment failures. By utilizing maintenance technologies such as motor circuit analysis, additional thermal imaging, and thermal monitoring sensors, organizations can improve machine asset availability and enhance the performance of monitoring equipment.
Integrating all maintenance data into a unified computer system enables the seamless sharing of information. In contrast, maintenance technicians and human resources play a crucial role in implementing these strategies and ensuring the effectiveness of maintenance programs.
Transitioning maintenance resources from reactive to proactive strategies helps avoid excessive additional maintenance efforts and reduces the risk of costly engine failure. These approaches are especially valuable in data centers and electrical maintenance, where continuous monitoring and proactive maintenance are essential for operational reliability and safety.
The sensors have been designed and built to withstand the challenging environments typical of applications such as ladle monitoring and Electric Arc Furnace monitoring.
Rather than rely on time-based physical inspections or reactive maintenance strategies, steel plants can take a proactive approach that improves asset utilization, enhances workplace safety, and mitigates the risk of catastrophic equipment failure.
To see how you can deploy Continuous Thermal Monitoring solutions in your facilities, download our latest white paper: Mitigating Risk in the Steel Industry – The Benefits of Continuous Thermal Monitoring